Dyness Knowledge | Commercial storage cooling technology: an energy efficiency revolution that solves the problem of "thermal runaway"
-
Technical Blog
-
2025-05-23
-
Dyness
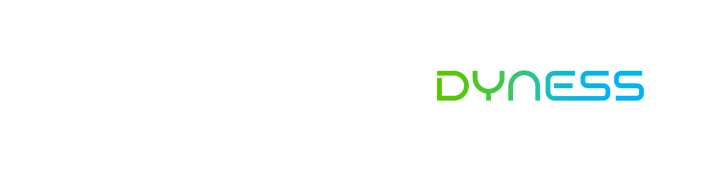
In the industrial and commercial energy storage (ICES) system, the life of the battery pack will be shortened by 50% for every 10°C increase in the operating temperature. With the explosive growth of industrial and commercial storage capacity driven by the dual carbon goals (the new capacity in 2024 increased by 47% year-on-year), how to break through the dual bottlenecks of "high temperature attenuation" and "thermal runaway" has become the core battlefield of the industry's technical breakthroughs.
The iteration of cooling technology is upgrading from the basic demand of "ensuring safety" to the strategic fulcrum of "enhancing asset value".
The efficiency limits and practical challenges of traditional cooling solutions
The current mainstream air cooling solution in the market (accounting for about 55%) relies on air convection to achieve heat exchange, and its inherent defects gradually become apparent in high-power scenarios.
Heat dissipation efficiency ceiling: At an ambient temperature of 40℃, the temperature difference of the battery cells in the air cooling system generally exceeds 5℃, and the temperature rise rate in local hot spots can reach 2℃/minute, far exceeding the battery safety threshold (≤1℃/minute).
Environmental adaptability shortcomings: Complex working conditions such as dust and salt spray can easily cause cooling fan failures. A third-party agency test shows that the average annual maintenance frequency of air cooling systems in coastal areas is 3.2 times, and the operation and maintenance cost accounts for 23% of the full cycle expenditure.
Energy efficiency paradox: In order to cope with peak heat dissipation requirements, the air cooling system is often in an "over-cooling" state. The cooling energy consumption of some projects accounts for 18% of the total system power consumption, significantly reducing the overall energy efficiency.
Although liquid cooling technology (accounting for about 32%) controls the temperature difference within 3°C through medium upgrades, problems such as pipeline leakage risk (annual failure rate 0.8%-1.5%), coolant freezing point limitation (conventional solutions are applicable to temperatures ≥-10°C) and high initial installation costs (40%-60% more expensive than air cooling) still restrict its large-scale application.
Breakthrough Path of Next-Generation Cooling Technology
Material innovation drives performance leap
The engineering application of phase change materials (PCM) opens up a new dimension of "passive heat dissipation". The graphene composite phase change material developed by a leading enterprise can quickly absorb latent heat at 45°C, control the temperature fluctuation of the battery surface to ±1.2°C, and cooperate with the microchannel liquid cooling plate to form a "solid-liquid two-phase heat transfer network", which reduces the heat dissipation thermal resistance by 60%. This "passive pre-cooling + active precision control" composite solution has reduced the average temperature of the battery cell from 52°C to 38°C in summer in a commercial and industrial energy storage project in Chongqing, and extended the cycle life by 22%.
Structural Optimization in Fluid Mechanics
Immersion liquid cooling technology breaks through traditional limitations through flow channel reconstruction. The new "honeycomb" liquid cooling chamber design improves the uniformity of the coolant flow rate by 40%, and with environmentally friendly coolant with a dielectric constant ≥ 25 (insulation level up to 10^14Ω・cm), 360° heat exchange of the battery cell without dead ends is achieved. Actual measured data shows that the temperature difference of this solution is stable at ≤1.5℃ in a wide temperature range of -20℃~60℃, and no additional heating device is required, saving 15% energy consumption compared to traditional liquid cooling solutions.
Digital Twins Enable Intelligent Temperature Control
The integration of edge computing and digital twin technology has upgraded the cooling system from "responsive control" to "predictive regulation". By deploying 100+ temperature sensors to build a battery thermal model, the AI algorithm can predict the risk of thermal runaway 15 minutes in advance. And dynamically adjust the cooling strategy: increase the coolant flow by 30% during the peak charging period, switch to energy-saving mode at night when the load is low, and increase the system's comprehensive energy efficiency ratio (COP) to 5.2, saving 35% of electricity compared to traditional solutions.
The technological breakthrough of Dyness
As a participant in industry innovation, Dyness has launched the Intelligent Hybrid Cooling System (IHCS) based on its deep understanding of industrial and commercial storage scenarios. Its core advantages are reflected in three dimensions.
Intelligent Temperature Control
Driven by a self-developed intelligent program and equipped with an adaptive PID control algorithm, dynamic and precise regulation of the cooling unit can be achieved. The system can calculate and adjust parameters in real time according to preset heat dissipation requirements, drive the cooling unit to respond quickly and operate stably under target conditions, and build a precise and efficient heat dissipation regulation system with intelligent control logic.
Energy Optimization
Equipped with a self-developed energy management module, the system can dynamically adjust the cooling strategy according to the load curve and ambient temperature.
Modular Design
Each module adopts standardized interfaces and plug-and-play design, which significantly improves the convenience and accessibility of operation and maintenance. At the same time, it is equipped with an intelligent monitoring system to support real-time collection of full-process operation data, online visual monitoring and remote maintenance intervention, and build an efficient operation and maintenance system for the entire life cycle from module-level maintenance to system-level management.
The future of the industry: a paradigm shift from “temperature control” to “value temperature control”
With the implementation of the mandatory requirement of the "New Energy Storage Project Management Specification" for battery temperature difference ≤ 2°C, cooling technology is changing from "optional configuration" to "core competitiveness". GGII data shows that in 2024, the premium rate of industrial and commercial storage projects with intelligent temperature control functions has reached 15%, and the order conversion rate of technology-leading companies has increased by 28%.
For Dyness, IHCS is not only a carrier of technological achievements, but also a practice of the concept of "scenario-defined technology" - by deeply deconstructing the differentiated needs of industrial and commercial users in scenarios such as peak-valley arbitrage, backup power supply, and demand management, the cooling technology is deeply coupled with the energy management, safety protection, and operation and maintenance system of the energy storage system to achieve the upgrade from "controlling temperature" to "creating value". In the journey of the energy storage system evolving towards "high integration, high reliability, and high yield", the ultimate goal of cooling technology is not only to "prevent the battery from overheating", but to ensure that the storage and release of each kilowatt-hour of electricity are in the optimal energy efficiency range.